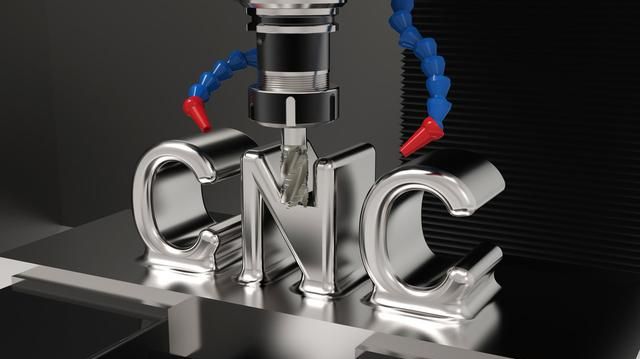
1. How To Divide The Processing Process?
The division of CNC machining processes can generally be carried out as follows.
A. Tool concentration division method It is to divide the process by the tool used, using the same tool to finish machining all the parts on the part that can be completed. In the use of the second tool, the third to complete the other parts they can complete. This can reduce the number of tool changes, compress the empty journey time, reduce unnecessary positioning errors.
B. To processing parts in order for the processing of many parts, according to its structural characteristics of the processing part into several parts, such as internal shape, shape, surface or plane. Generally, first processing plane, positioning surface, then processing holes; first processing simple geometry, then complex geometry; first processing lower precision parts, then processing higher precision requirements of the parts.
C. To roughing, finishing sub-sequence method for easy processing deformation of the parts, due to roughing may occur after the deformation and the need for calibration, so generally speaking, where roughing, finishing are to separate the process. In summary, in the division of the process, must depend on the structure of the parts and process, the function of the machine tool, the number of parts CNC machining content, the number of times the installation and the production organization of the unit flexible control. Another proposal to use the principle of process concentration or the principle of process dispersion, according to the actual situation to determine, but must strive to rational.
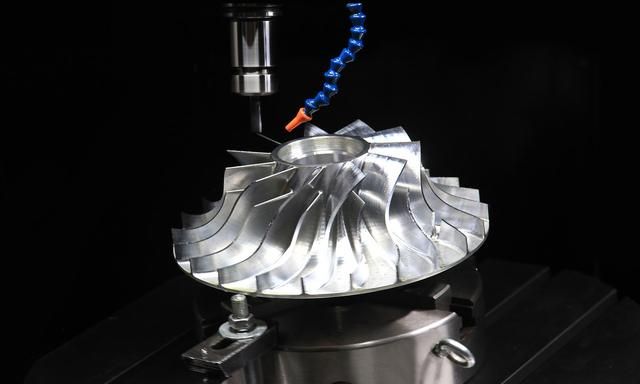
2. The Workpiece Clamping Method Should Pay Attention To Those Aspects
In determining the positioning reference and clamping scheme should pay attention to the following three points.
A. Strive to design, technology, and programming calculations of the benchmark unity.
B. Minimize the number of clamping, as far as possible in positioning can be processed after all the surfaces to be machined.
C. Avoid the use of a manual adjustment program to occupy the machine.
D. Fixture to open smoothly, its positioning, clamping mechanism can not affect the processing of the tool (such as collision), encounter such cases, can be used with a vise or add the base plate to draw the screw way to clamp.
3. How To Determine A Reasonable Point For Tool Setting?
A. The tool setting point can be located on the machined part, but note that the tool setting point must be the reference position or the part that has been machined, sometimes the tool setting point is destroyed after the first process, which will lead to the second process and the subsequent tool setting point can not be found, so pay attention to the first process of tool setting to set up a relative tool setting position in a place with a relatively fixed dimensional relationship with the positioning reference, so that they can be found according to their relative position. Therefore, in the first process of tool setting, it is necessary to set up a relative tool setting position at the place where there is a relatively fixed dimensional relationship with the positioning reference. This relative tooling position is usually located on the machine table or fixture. The selection principles are as follows.
(1) Easy to find the correctness.
(2) Easy to program.
(3) The tool setting error is small.
(4) Easy to check during processing.
B. The origin position of the workpiece coordinate system is set by the operator himself, it is in the workpiece after clamping, through the tooling to determine, it reflects the distance between the workpiece and the machine zero position relationship. Once the workpiece coordinate system is fixed, generally do not change. Workpiece coordinate system and programming coordinate system both must be unified, that is, in processing, the workpiece coordinate system and programming coordinate system are the same.
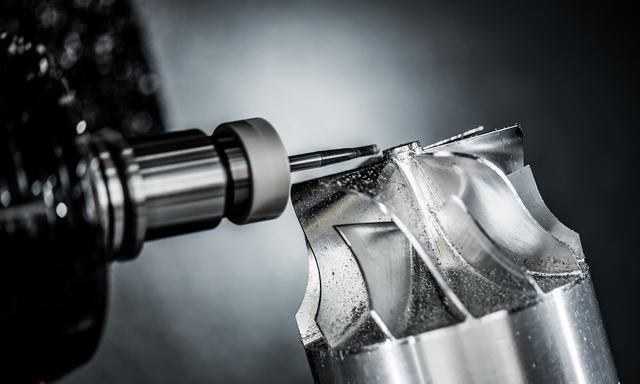
4. How To Choose The Tool Path?
The tool path is the trajectory and direction of the tool relative to the machined part during the index-controlled machining process. The reasonable choice of machining route is very important because it is closely related to the machining accuracy and surface quality of the parts. In determining the tool path is to consider the following points:
A. To ensure the machining accuracy of the part.
B. Facilitate numerical calculation, reduce programming workload.
C. Seek the shortest machining route, reduces the empty tool time to improve machining efficiency.
D. Minimize the number of program segments.
E. Ensure the roughness of the workpiece contour surface after machining, the final contour should be arranged to be continuously machined by the last tool.
F. The tool entry and exit (cut-in and cut-out) routes should also be carefully considered to minimize the stopping of the tool at the contour (sudden change of cutting force causing elastic deformation) and leaving tool marks, and also to avoid the vertical undercutting on the contour surface and scratching the workpiece.

5. How To Monitor And Adjust During The Machining Process?
After the workpiece is corrected and the program is debugged, it can enter the automatic processing stage. In the automatic machining process, the operator should monitor the cutting process to prevent the abnormal cutting from causing workpiece quality problems and other accidents. The cutting process is monitored mainly considering the following aspects.
A. Machining process monitoring rough machining is mainly considered the workpiece surface of the excess margin of the rapid removal. In the automatic machining process of the machine tool, according to the set cutting amount, the tool automatically cutting according to the predetermined cutting trajectory. At this time, the operator should pay attention to the cutting load table to observe the cutting load changes in the automatic machining process, according to the tool bearing force conditions, adjust the cutting amount, to maximize the efficiency of the machine tool.
B. Cutting process cutting sound monitoring in the automatic cutting process, generally start cutting, the tool cutting workpiece sound is stable, continuous, brisk, when the machine tool movement is smooth. As the cutting process proceeds, when there are hardpoints on the workpiece or tool wear or tool feeding clamps and other reasons, the cutting process appears unstable, unstable performance is a change in the cutting sound, the tool and the workpiece will appear between the sound of mutual impact, the machine will appear vibration. At this time should be a timely adjustment of cutting dosage and cutting conditions, when the adjustment effect is not obvious, the machine should be suspended, check the condition of the tool and workpiece.
C. Finish machining process monitoring finish machining, mainly to ensure the workpiece machining size and surface quality, cutting speed is higher, the feed amount is larger. At this time, attention should be paid to the impact of the chip tumor on the machined surface, and for the cavity processing, attention should also be paid to the corner processing overcut and let the tool. For the solution to the above problems, one is to pay attention to adjust the spraying position of the cutting fluid, so that the processing surface is always in the best cooling conditions; second, we should pay attention to the observation of the quality of the machined surface of the workpiece, through the adjustment of the cutting amount, as far as possible to avoid changes in quality. If the adjustment still has no obvious effect, the machine should be stopped to check whether the original procedure becomes reasonable. Special attention should be paid to the position of the tool when pausing to check or stopping to check. If the tool is stopped in the middle of cutting, the sudden spindle stop will cause tool marks on the surface of the workpiece. Generally, stopping should be considered when the tool leaves the cutting state.
D. Tool monitoring. The quality of the tool largely determines the machining quality of the workpiece. In the automatic machining cutting process, the normal wear condition and abnormal breakage of the tool should be judged by sound monitoring, cutting time control, pause check during cutting, workpiece surface analysis, etc. According to the processing requirements, the tool should be processed in time to prevent the processing quality problems arising from the tool not being processed in time.
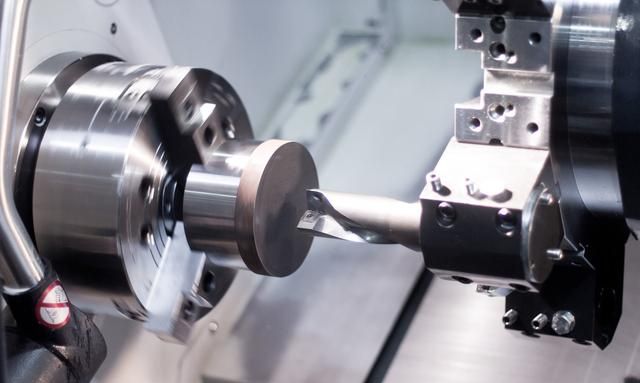
6. How To Reasonably Select The Processing Tool?
A. When milling the plane, you should choose not to resharpen carbide end mills or end mills. When milling in general, try to use the second walking tool processing, the first walking tool is best to use the end mill rough milling, along the surface of the workpiece continuous walking tool. The width of each walk is recommended to be 60% – 75% of the tool diameter.
B. End mills and end mills with carbide inserts are mainly used for machining tabs, recesses, and box mouth surfaces.
C. Ball cutters and round cutters (also known as round nose cutters) are commonly used for machining curved surfaces and beveled contour profiles. And the ball cutter is mostly used for semi-finishing and finishing. The round cutter with carbide tools is mostly used for roughing.
7. What Is The Role Of The Processing Program Sheet?
A. Machining program sheet is one of the contents of the CNC machining process design, is also required to comply with the operator, the implementation of the protocol, is a specific description of the processing program, the purpose is to allow the operator to clarify the contents of the program, clamping and positioning, each processing program selected tool and should pay attention to the problem.
B. In the machining program list, it should include: drawing and programming file name, workpiece name, clamping sketch, program name, the tool used in each program, the maximum depth of cut, the nature of machining (such as roughing or finishing), theoretical machining time, etc.
8. What To Do Before The CNC Programming?
After determining the machining process, before programming to understand.
A. The workpiece clamping method.
B. The size of the workpiece blanks —- to determine the scope of machining or whether multiple clamping is required.
C. The material of the workpiece —- to choose which tool to use for the machining.
D. What tools are in stock —- to avoid having to modify the program due to the unavailability of this tool during machining, or to prepare in advance if this tool must be used.
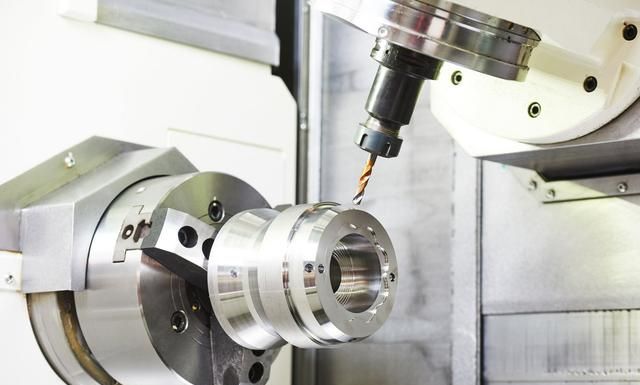
9. What Are The Principles For Setting The Safety Height Of Programming?
The principle of setting the safety height: generally higher than the highest surface of the island. Or the programming zero points are located in the highest surface so that you can also minimize the risk of collision with the tool.
10. Why Do Toolpaths Still Need To Be Post-Processed?
Because different machine tools can recognize the address code and NC program format is different, so to choose the correct post-processing format for the machine used to ensure that the program can be run.
11. What Is DNC Communication?
Program delivery can be divided into CNC and DNC, CNC refers to the program through the media (such as floppy disks, tape readers, communication lines, etc.) to the machine memory, processing from the memory to call out the program for processing. Because the capacity of the memory is limited by the size, so when the program is large, you can use the DNC method of processing, because the DNC processing machine directly from the control computer to read the program (that is, while sending to do), so the capacity of the memory is not limited by the size.
The above are the 11 tips of CNC programming in CNC machining basics, hope it can help you, and welcome to communicate if there is a lack of places.